旅立ちの日に
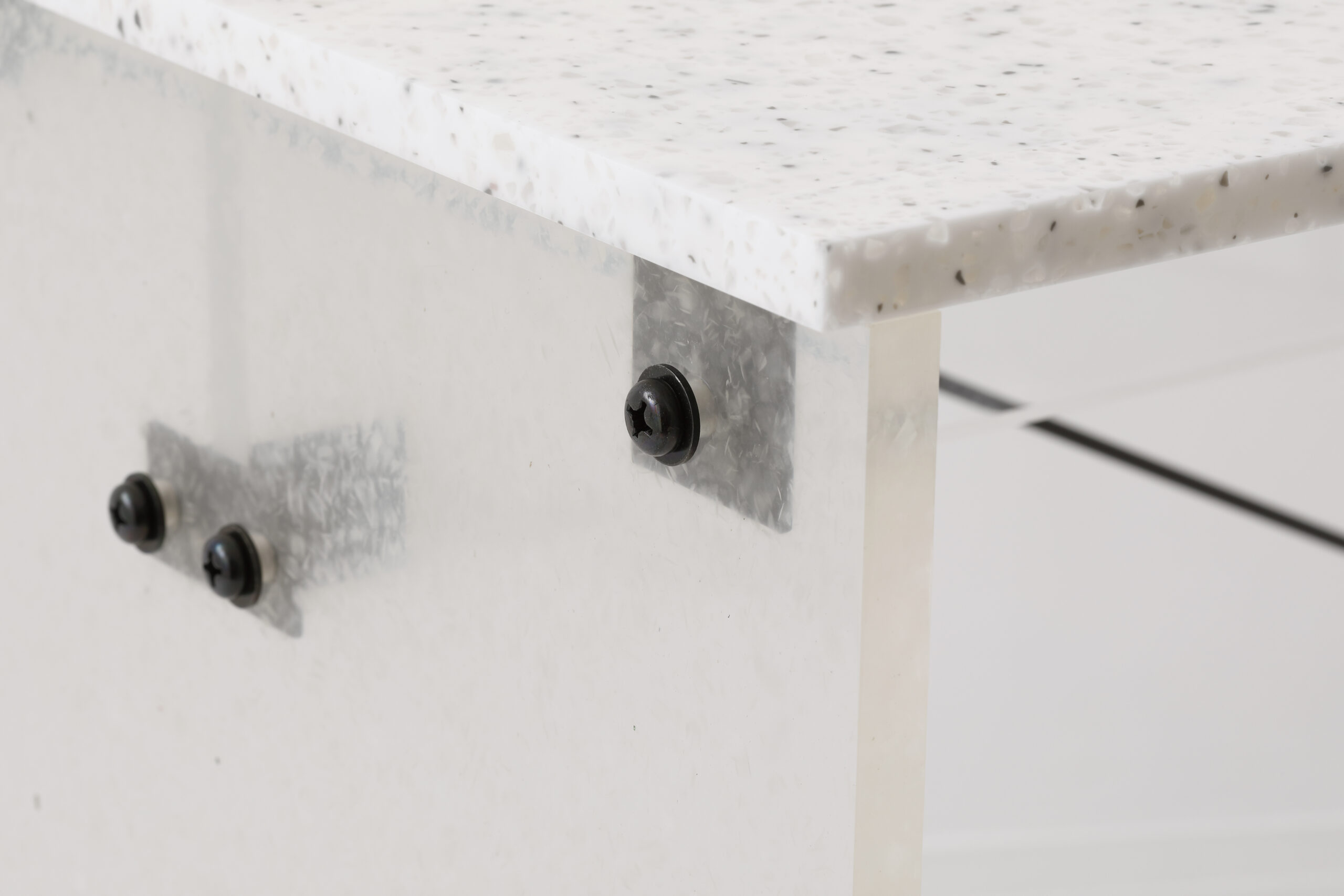
「3.11」の東日本大震災から11年が経過しました。この期間に「安全」「平和」「当たり前の日常」というものが「当たり前では
ない」ことを多くの人が感じたのではないでしょうか?コロナ禍やロシアの戦争が起こったことによりさらにその思いは増して
来ていると予想されます。
「当たり前」が「当たり前ではない」と言うこと、それは「資源」や「環境」にも言えると思います。限りある資源と環境汚染に
ついて考えた場合はやはりサスティナブル又はSDGsの考えを一人一人が意識して、実践して行く必要があるのだと改めて
思いました。
今回はプラスチックマーケットの協力工場である静岡県のアート日向に出向き、昨年秋の展示会で発表した封入再生材の什器一式を
ある企業様が新店用什器として購入されましたので、検品・梱包して持ち帰りました。この什器の「サスティナブル」のコンセプト
に共感頂いた形になります。昨年秋の展示会の様子や封入再生材に関する記事は下記の通りとなります。
https://plasticmarket.co.jp/column/placycle%e3%82%b9%e3%82%bf%e3%83%bc%e3%83%88%ef%bc%81/
アート日向から持ち出した「封入再生什器」をお客様の倉庫に無事納品。新店に向けて旅立つ「封入再生材什器」を見送りました。
新店がオープンしましたら、許可は頂いているので改めてこのサイトでアップしてご紹介させて頂こうと思います。
この封入再生材についてはすでにサスティナブル又はSDGsを意識したセレクトインテリアショップ様や建材・住宅設備メーカー様
から新商品開発のお声がけを頂いており、製作進行しております。こちらも商品化になりましたら随時ご紹介させて頂けたらと思い
ます。
そしてアート日向と言えばそのアクリル加工の美しさに定評があり、今までも様々な自社プロダクトやブランド様からご依頼の
商品やディスプレイを製作して参りました。そのアクリルの美しさの最終仕上げが「磨き」加工となるのですが、
本日はその「磨き」加工仕上げを長年行っている職人Kさんにもお話をうかがうことができました。
もともと自営で竹細工のお土産を製作されていて、その後サッシの工場に転職して工場長になったものの会社が倒産してしまい、
知り合いの伝手でアート日向に来られたのが15年ほど前とのこと。サッシは硝子や金物との組み合わせでその重さや取扱の
面倒さがあったもののアクリルは軽くて単一素材での納品が大半だったため、最初は非常に楽に感じたそうです。
一通りの加工を経験して、最終的に「磨き」部門を担当して今に至るKさんは年齢は70を超えますが、他の職人さんから
その「磨き」の腕や技術は一目置かれ、唯一無二な存在となっていると聞きます。
「磨き」と一言で書いておりますが、その前工程で「研ぎ出し」という作業が入ります。アート日向の製作物は三次元切削物が
多く、切削した刃物跡をヤスリで取り除く作業が必要になります。ヤスリの番手を徐々に上げて丹念に凹凸を無くして行く作業。
地味に見えますが、非常に神経を使う作業と言えます。
「研ぎ出し」が終わったら次は「磨き」です。完成品の大きい小さいによって使用するバフの機械は違います。
完成品が大きい物、たとえば家具や大きな柱状の物ならハンディタイプのバフを用い、持ち運べるサイズの物は壁に備え付けてある
タイプのバフを使用します。いずれもヘッドの回転部分に研磨剤をまぶして磨いて行きます。
磨きは「程度」が難しく、磨き過ぎると「ダレ」という形が崩れる症状やクラックが発生してしまいます。
そのあたりのさじ加減をうまく調整する必要がある訳ですが、今までどのような物の「磨き」が大変だったかったのかをKさんに
お聞きしてみました。
1.凹凸の多い立体的な家具脚(大きい)
→曲面は研ぎ出しが大変で、角が残る面はダレないようにするのが大変だそうです
2.ポケットがたくさんあるディスプレイ(大きい)
→ポケット内は熱で磨く別の方法が取られますが、非常に手がかかるそうです
3.5t以内で肉薄のイヤーカフ(小さい)
→小さいので研ぎ出しも磨きも大変だそうです
その製造物の価値を最後に決定づける「磨き」工程はアクリル素材の美を追求する上で欠かせない工程になります。
そんな大事な加工を担うKさんとその技術を引き継ぐ中堅や若手によってアート日向の技術はさらに磨かれていくと思われます。